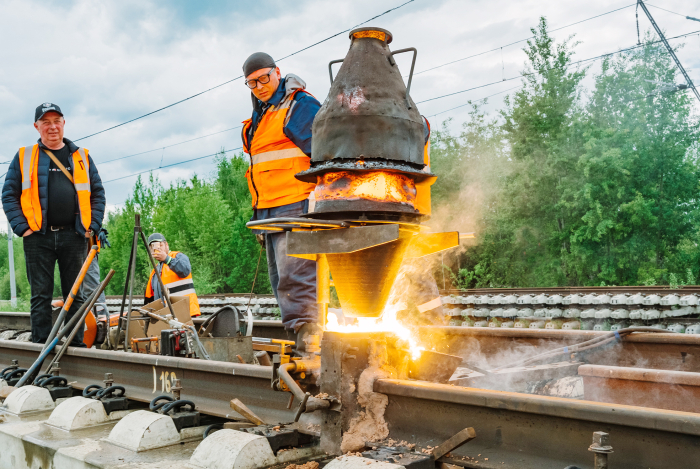
Автор фото: Бронислав Сурин/ИД «Гудок»
Процесс сварки организовали Департамент технической политики совместно с Управлением пути и сооружений Центральной дирекции инфраструктуры и Центральной дирекцией по ремонту пути. Учитывая высокий трафик на будущей первой высокоскоростной магистрали страны, необходимо разработать принципиально новые методики ремонта и восстановления рельсового полотна. Путевая рельсосварочная самоходная машина провела сварку рельсов контактным способом, а бригада ремонтников – термитным с использованием специальной смеси и тигля. С помощью специальной краски учёные определили температуру в разных зонах стыка во время этого процесса. Это важно для понимания свойств металла после сварки. Также были демонтированы рельсовые образцы, сваренные ещё в октябре прошлого года и прошедшие полноценную нагрузку на безбалластном экспериментальном участке. ВНИИЖТ проведёт их углублённые лабораторные исследования, которые включают в себя оценку статической прочности и металлографический анализ сварных соединений.
По словам начальника отдела сварки, наплавки и шлифовки рельсов Управления пути и сооружений Виктора Романенко, при проведении ремонтных работ будет сделан акцент на использовании проверенных временем технологических решений, адаптированных к особенностям безбалластной конструкции.
«В частности, в апреле 2025 года был утверждён технологический процесс для опытного применения по восстановлению целостности рельсовых плетей на безбалластном пути с использованием путевой рельсосварочной машины при оптимальной температуре рельсовой плети, – рассказал Виктор Романенко. – Вместе с тем для оперативного и качественного проведения ремонтных процессов требуется составление и утверждение ряда дополнительных нормативных документов, а также проведение работ по нормированию времени».
На безбалластном пути для контактной сварки и последующей шлифовки стыка нужно обеспечить достаточное рабочее пространство в районе стыка. Московская дирекция по ремонту пути (ОПМС-68) создала опытную проставку, которая локально поднимает плеть на 100 мм над поверхностью бетона. Её также испытали в процессе сварки. Проставка располагается в точках, соответствующих 3-й и 9-й шпалам от сварного стыка, обеспечивая необходимый зазор для подвесной сварочной головки и проведения сварочных работ. Это очень хорошее адаптивное решение, учитывающее специфику конструкции БВСП. А для шлифовки подошвы рельса в районе стыка требуется подъём плети уже на 200 мм, но разработка московских путейцев позволяет и это, обеспечивая здесь пространство для работы электрошлифовальным станком типа СЭШ-У. Использование лёгкого и стандартного оборудования снижает трудозатраты и сокращает время ремонта, что для ВСМ очень важно.
Никакое из тех государств, которые владеют технологией высокоскоростного движения, не делится знаниями по этой теме, поэтому всё приходится разрабатывать и испытывать самостоятельно.
«Для того чтобы обеспечить скоординированный подход к развитию сварочных технологий и поддерживать высокий уровень безопасности движения на ВСМ, создана и функционирует специальная рабочая группа по сварке на площадке Департамента технической политики, – отметил ведущий специалист отдела качества и диагностики департамента Александр Спащенко. – Её представители проводят поисковые исследования перспективных технологий и технических решений и представляют рекомендации к внедрению в технологические процессы, разрабатывают и актуализируют стандарты, нормативную документацию, занимаются также повышением квалификации персонала, занятого в сварочных процессах. Учёт специфических условий эксплуатации на участках пути, где скорость движения поездов достигнет 400 км/ч, является критически важным для безопасности перевозок по ВСМ».